粉末射出成形(PIM)は複雑形状のnear-net shapingプロセスとして近年盛んに開発が行われている。PIMは、金属粉末の流動性と成形品の保形性を得るために、40vol%に及ぶ樹脂・ワックスによるバインダーとの混合材料を用いる。この粉末・バインダー混合体ha強い非線形流動を示し、成形体のクラックや表面欠陥などを引き起こす大きな原因となる。成形精度の向上のためには、内部粉末の分散状態を考慮の上、粉末・バインダー混合材料の流動性を正確に予測する必要がある。しかしPIMは閉金型を用いるため、内部の材料変化の直接観測は困難であり、数値計算によるシミュレーションは最も効果的な手法と言える。本研究では、個々の粉末とバインダーの動きを考慮した微視的なモデル「粒状体モデル」と、平滑化と構造化による中間的なモデル「平滑化モデル」の2つのレベルの粒子系解析法を示し、PIMプロセスで用いられる粉末・バインダー混合材料の内部構造を考慮した流動特性評価を試みる。 粒状体モデル 本解析で用いる粒状体モデルは、FEM/FDMによる固体・流体解析手法とは異なり、個別要素法などの粒子系解析モデルを基本としている。このモデルでは、粉末およびバインダーの微視的な相互作用を考慮し、粉末Core/バインダーShellの複合要素を用いて粉末・バインダー混合体を表現している。粉末粒子iの変位は、周囲の粉末粒子jからの相互作用力の平衡から、運動方程式  を時間積分する事で計算する。ここで、miは粉末粒子iの質量、 、 はそれぞれ粉末・バインダー間相互作用、粉末粒子間相互作用である。前者は、粉末とバインダーの間の粘性項、後者は粉末同士が接触する際の弾性反発力として個々の要素間で計算される。  また、異形状粉末の影響を考慮するために、複数の粉末粒子を結合した連結要素を用いる。粒子要素を連結する事により、何らアルゴリズム等の変更もなく任意の形状の粉末を表現する事が可能となる。 平滑化モデル 粒状体モデルはその仮定ゆえに実スケールの大規模な解析や微小粉末を構成要素に持つ材料では、膨大な量の計算リソースが必要となる。このため、セラミックス射出成形の様に微小粉末を扱う場合では、そのままのモデルでの適用は難しい。 平滑化(smoothing)モデルは、上記の問題に対して、粒子分布を平滑化マッピングすることで、ある程度粒子分布の影響を保持しつつ連続体的に方程式の処理を可能にしている。粉末粒子は粒子群(super particle)として扱われ、連続体上の節点値にマッピングされる。現在のモデルにおける平滑化手法は、kernel関数によって質量重み平均を行い、各物理量を空間上にマッピングする。  ここで、Wは平均化kernel関数、hIは平滑長さを表す。 混合材料内の相互作用は、粒状体モデルと同様に粉末・バインダー間による粘性力Fbと粉末同士の接触力Fcを仮定する。各粒子について応力が一様に分布すると仮定すると、各粒子iにおける応力 iは以下の様に定義できる。  ここで、Lijは粒子間位置ベクトル、DiとCiは見かけの粘性と剛性マトリクスである。構造化された粒子群Iの応力SIは以下の様に表せる。 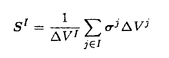 以下のシミュレーションでは、既知のランダム配置から粒子群の構造を規定し、そのサンプリングから上記の様に構造化された物理量を計算する。 表1: Computational condition of capillary viscometer tests. 図1: Comparison between calculated and experimental viscosity results of capillary viscometer tests. 構造化された物理量のマッピングにより、支配方程式は以下の様に書き下せる。  粉末・バインダー混合体の粘性評価 キャピラリーおよび平行プレートによる粘性試験のシミュレーションを通して、粉末特性の違いによる粘性挙動の変化について調べ、粉末の微視的な特性が巨視的な粘性にどのように影響するかを考察する。Table.1に示す条件の下に、キャピラリー試験シミュレーションを行い、同条件の実験結果と比較した。Fig.1は、せん断ひずみ速度 aとみかけの粘度 a関係について計算・実験の両結果をプロットしたものである。ここでは、両者は定量的にもかなり一致しており、金属粉末・バインダー混合物が概ねべき乗則流体として振舞う事が分かる。また、計算結果から壁面すべり速度を求めると、実験で求めたすべり速度とほぼ一致した非線形な関係が得られた。さらに、管径方向の速度分布を求めると、ひずみ速度に応じて形状が平らに変化し、従来の研究でも報告されているように高ひずみ速度においては栓流(Bingham流体)に近い挙動をすることが分かった。 同じ粉末体積率であっても、粉末粒径を分布させる事で流動特性を向上させる事が出来る。Fig.2は、同じ粉末・バインダー材料において2種類の大きさの粉末を混合させた場合の平行プレート試験の計算結果である。小さい粉末がいわば潤滑のような役割を演じるために、平均粒子間距離(粒子のmobility)の増加に伴う粘度の低減が確認された。 次に平滑化モデルを用いて、粉末の絶対粒径による違いを検証した。Fig.3は、三種類の粒径を持つ粉末材料を用いた数値実験の計算結果を示している。縦軸は均一な非凝集系の粘度により正規化された粘度 0(= / u)であり、粒子の凝集密度を表している。粉末粒径が小さくなるに従ってより高い相互作用を示している。すなわち、微小粉末粒子の凝集が粘性を急激に増加させている事が確認された。 以上の粘性試験シミュレーションにより、粉末の凝集は粘度の増加を引き起こし、粉末mobilityの増加は粘性の減少を引き起こす事が分かった。粉末粒径や粒径分布・体積率・形状などはこれらを制御する主な要因であり、粉末・バインダー混合材料の粘性挙動に、大きく影響していることが計算の面からも明らかとなった。 図2: Calculated relative viscosity of the bimodal distributed powder compounds. 図3: Calculated normalized viscosity of various powder diameters.流動シミュレーション 実際の成形プロセスでは、クラックやその他の欠陥の予測が最も必要とされる。ここでは、流動中における金型内の粉末密度の分布を予測し、流動性とクラックの関連性について考察する。 Fig.4は、金型充填シミュレーションの成形中の粉末密度分布を別々の2方向から示した図である。ここでは初期粉末密度で正規化した相対密度を示している。粉末は外側角A部において凝集し、ゲート入口付近と内側角B部分においても、凝集部と希薄な部分が確認された。 この内側角B部は、実際の製品においてクラックが多く現れる箇所である。こうした材料内部での疎密化は、外側角A部での凝集によって粘性的に不安定が生じ、流れの方向を変えるために引き起こされている。 図4: Normalized density distributions in the case of monosized powders. 粒径をR-R分布させた材料を用いて同じ条件で解析を行うと、角部における疎密化が単一径材料と比較して緩和された。粉末粒径を分布させる事により全体の粘度を低下させ、歪み速度依存性を抑えることができるためである。この様な粉末粒子の状態の違いはクラックなどの原因となる粉末の不均一な分布の発生メカニズムに関わる問題であろう。 Fig.5は、半行プレートせん断流れにおける表面上の粉末体積分布の時間変化を表している。粉末分布の多少の偏りが、粉末の凝集を引き起こして行く様子が分かる。半面と粉末との幾何学的な関係上、表面境界付近は内部と比較してバインダーの体積率が高くなっている。このため、せん断流れのような圧力効果の低い流れでは、粉末同士の相互作用により容易に粉末凝集が起こりやすくなると考えられる。 図5: Development of agglomeration of powders on the surface in the parallel plate flow.結言 PIMプロセスで用いられる粉末・バインダー混合材料における流動充填挙動を調べるための数値モデルとして、ミクロレベルの個別解析モデルである粒状体モデルと、連続体との中間的な平滑化粒子モデルの構築を行った。キャピラリー試験やせん断流れのシミュレーションにより、従来の実験結果と同様に、せん断ひずみ速度と見かけ粘度の間に非線形な関係が確認され、粉末粒径・粒径分布などの微視的な材料特性が巨視的パラメタにも大きな影響を持つ事が示された。さらに、充填流動シミュレーションでは、金型内や表面上での欠陥生成のメカニズムが、混合材料の流れに伴う粉末の凝集・離散によって発生し得る事が示された。 粉体特有の非線形な欠陥生成メカニズムを予測するには、粒子系モデルの様に微視的な相互作用から構築した数値モデルによる解析は不可欠であろう。また、本手法は粉末の微視的な情報を保持しているので、充填プロセス条件の最適化のみならず、脱バインダー・焼結の直接解析・評価への応用が期待できる。 |