内容要旨 | | 1.はじめに 歯車やころがり軸受などころがり接触をする機械要素は長時間負荷運転されると,表面に剥離やクラックなどの損傷を生じる.このような損傷は一般にころがり疲れ損傷と言われている.ころがり疲れ寿命はすべり率との関係が認められているが,またすべり率と接線力の間には強い相関が認められ,ころがり疲れに対する実質的なパラメータとしては接線力を考えるべきであろうと思われる.このような観点から本研究においては接線力係数の広い範囲にわたってころがり疲れ寿命を実験的に求め,接線力ところがり疲れ寿命の関係を導くことにより,ころがり疲れ寿命のメカニズムを説明する. 表1 試験片および試験条件2.試験機・試験片・試験条件 本研究で用いた試験機は二円筒試験片を用いるアムスラー摩擦試験機である.試験片データ,試験条件などを表1に示す. 3.転走面における円周方向最大塑性流動量Y,最大加工硬化量 および加工硬化量 uに及ぼす接線力係数の影響 下試験片転走面軸方向に0.25mm間隔でつけたマイクロビッカース圧痕が接触の繰り返しにより円周方向への変位量を測定しその最大値を転走面における円周方向最大塑性流率動量Yとした.また試験後の材料内部深さ方向の硬さの分布を求めることによって,負荷の繰り返しによって材料内部に生じた加工硬化を求めた.材料内部の加工硬化の深さ方向分布における最大値を最大加工硬化量 ,同じ分布線図において,試験前硬さ直線と試験後硬さ分布曲線で囲まれる面積を加工硬化量 uと定義しY, および uのNおよびT/Wに対する変化を求めた.それらの関係はいずれの試験片硬さにおいても次の実験式(1)〜(3)のように求まった.  4.ころがり疲れ寿命NLにおよぼす接線力係数の影響 実験で得られたころがり疲れ寿命NLとT/Wの関係を図1に示す.T/Wの変化に対するNLの特性はT/W>0の領域から,T/W<0の領域にかけて連続的に増加するが,T/W<0のある一定値からさらに小さい値を取る領域では,逆に減少に転ずる.この定性的な傾向は材料の硬さに無関係に成り立つことが今回の実験結果より明白になった.T/Wの減少に伴い,NLが増加から減少に転ずるT/Wの値は,いずれの材料硬さにおいにても-0.05付近の値を取っている. 図1 ころがり疲れ寿命のT/W特性5.塑性流動と加工硬化の関係 大きな塑性歪を対象とするとき応力-歪の関係は,n乗硬化則( =k n)が一般に用いられている.せん断歪 と との関係にも,n乗硬化則がそのまま成立すると仮定するとk,nを定数として式(4)が得られる.ここで,i回接触時の歪増分△ i(z)は加工硬化の進行によってiの増加に伴い絶対値は減少するが,その減少率はzに無関係に一定であると仮定すると式(5)〜(7)の各式が誘導される.ここで,実験式(1)と(7)式を等値することによって式(8)が得られる. 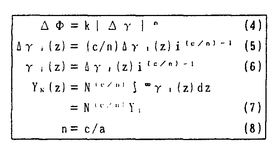 6.ころがり疲れ寿命に対するManson-Coffin則の援用 一般の材料の,低繰り返し数疲れに対して塑性歪振幅△ と疲れ寿命NLとの関係を与えるManson-Coffin則が知られている.ここでは,第一近似としてころがり接触面の疲れ現象にもManson-Coffin則およびそこから派生したYao-Munse則が成立することを仮定すると式(9)が得られた.ここではe=1,△ rは1サイクルで破壊が生じるせん断歪である.  7.転走面下におけるせん断塑性歪 材料の機械的性質と前述した実験における接触条件を用いて,転走面下のせん断歪増分△ i(z)を数値計算により求めた.なお,この計算は志摩政幸氏の協力によるものである.計算の結果を図2に示す.T/W≧0では深さz/b=0.5のあたりで最大値(ピーク(1))を取る.このピークの高さは,T/Wの増加とともに増大して行く.T/W<0になると,ピーク(1)の高さが次第に減少する.一方縦軸の値で0〜0.5および1程度のあたりに逆符号のせん断歪,ピーク(2),(3)が現れ,その絶対値の増加とともに増大して,T/W=0.10附近を境にピーク(1)よりも大きくなる. 図2 せん断歪の深さ方向分布8.接線力係数ところがり疲れ寿命 ころがり疲れにおける破壊が,最大せん断塑性歪を生ずる深さにおける材料の低繰り返し数疲れによって生ずるものと考え,その部分のせん断塑性歪に式(9)を適用して,Dmが1に達した時にころがり疲れ寿命に達するものと仮定する.図2でせん断塑性歪の計算を行った各深さにおける各T/Wに対する△ i(z)の値を用いて,Dm=1となる接触回数N’を求め,T/Wの関数としてプロットすると図3が得られる.それぞれの深さにおけるN’の値は,T/W=-0.15〜0.15の範囲内に最大値を持ち|T/W|がさらに増加すると減少する傾向を示している.このように,一定の深さに対するN’の変化を示す曲線の全体的な特徴は共通しているが,N’が最大値をとるT/Wの値は,転走面からの深さによって異なりT/Wの関数としてのN’の変化は図3の曲線群の下側の包絡線で与えられる.図3の包絡線と実験から求められたNLのデータ(図1)をまとめて図4に示す図3の包絡線からから求められるN’曲線は実験データNLしてはほぼ同じ傾向が認められる.とくに寿命がピークを示すT/Wの値については,各材料硬さ毎に定量的にも実験データと合致している.ただ,寿命の値を較べてみると,Yao-Munseの仮説から推定した寿命は,実験から求まった寿命より短く,またT/Wに対する変化も実験の方が小さい.本解析の考え方によってころがり疲れ寿命の接線力係数による変化の定性的な特徴に一つの説明を宛てることが出来たが,接線力係数の影響には他の現象を介するものもあるように思われる. 図3 Yao-Munse則から推定されるころがり疲れ寿命N’ 図4 ころがり疲れ寿命の実験値NLと推定値N’の比較9.結論 三種類の熱処理を行った炭素鋼円筒のころがり-すべり接触の実験を行い,またその結果の説明に低繰り返し数疲れの理論を援用することにより次の結果を得た. (1)転走面における円周方向塑性流動量Y,加工硬化量 uの接触回数Nに対する実験式が得られた. (2)ころがり疲れ寿命がT/Wによって大きく変化し,T/W=+0.10〜-0.04の範囲では,T/W>0領域から<0の領域への変化に伴って,ころがり疲れ寿命が連続的に増加し,T/W<-0.04になると逆に減少に転ずることを示した. (3)接触の繰り返しに伴う加工硬化の進展により接触回数によって変化する円周方向塑性流動の単純化モデルを提案し,塑性流動と加工硬化量の実験式が,材料の加工硬化特性を介して関連づけられることを示した. (4)ころがり疲れを,転走面における低繰り返し数疲れと考え,Manson-Coffin則およびYao-Munseの仮説を援用して,加工硬化を考慮した場合のころがり疲れ寿命式を求めた. (5)加工硬化を考慮したせん断塑性歪の計算結果と上に求めた寿命式を用いて,T/Wところがり疲れ寿命の関係に定性的な説明を与えた. |
審査要旨 | | 工学修士似内昭夫提出の論文は,「ころがり疲れにおよぼす接線力の影響に関する研究」と題し,8章からなっている. 歯車やころがり軸受のようにころがり接触をする機械要素は,長期間運転すると接触面にはく離が生じ,これが振動の原因となって正常な運転ができなくなることがある.このような損傷はころがり疲れと呼ばれ,これら機械要素の信頼性・寿命を支配する因子の一つとなっている. ころがり疲れは,接触面に繰り返し作用するヘルツ圧と,通常併存するすべりにともなう接線力に起因する,表面層の疲れ破壊と考えられる.したがって単純に考えると,一定のヘルツ圧の下では,接線力が大きくなるほど寿命は短縮されるはずである.ところが従来から,少なくとも塑性流動を生ずるような比較的軟質の材料について,ドライバーすなわち相手を引きずる側の面に比べて,フォロワーすなわち引きずられる側の面のほうが,寿命がずっと短かくなることが知られている.本研究は,このような現象の解明を目的としている. 第一章は緒論で,ころがり疲れとそれが問題となる機械要素,ころがり疲れに関する従来の研究を概観し,本研究の目的と本論文の構成について述べている. 第二章では,ころがり疲れに関する実験の詳細を説明している.本研究では,上述の機械要素を模擬した二円筒試験機を用い,三種類の熱処理によって硬さを変えた炭素鋼の円筒を試験片として,硬化軸受鋼円筒との繰り返しころがり接触においてはく離を生ずるまでの寿命を,接線力係数の関数として求めている.ここで接線力係数と呼んでいる量は,接線力と垂直荷重の比であって,試験片がフォロワーの場合を正,ドライバーの場合を負と定義している. 第三〜六章は実験結果の記述に充てられており,まず第三章では,運転条件,潤滑油,試験片の材料などが異なる場合における,すべり率と接線力係数の関係を調べている. 続く第四章では,ころがり接触にともなって試験片に生ずる塑性流動について述べており,断面の観察により内部の流動状態を調べるとともに,代表値として表面中央に生じた円周方向の最大塑性流動量を選び,その値が接線力と直線的な関係にあって,ある負の接線力係数で0となることを示し,最大塑性流動量と接線力係数および接触回数との関係を表わす実験式を導いている. 第五章ではころがり接触の繰り返しによる加工硬化を取上げ,表面下における硬さの分布を調べて,接線力係数による変化を明らかにするとともに,硬さ分布曲線が囲む面積として定義した加工硬化量と,接線力係数および接触回数とを関係づける実験式を導いている. 第六章が,本研究の中心をなすころがり疲れ寿命に関する実験結果であって,接線力係数を+0.10から-0.14まで広く変化させると,正の範囲から負の範囲にかけて連続的に寿命が長くなるという従来の知見に加え,寿命は接線力係数-0.05の付近で最大値をとり,負の範囲でそれより接線力係数の絶対値が増加すると再び短くなること,さらに寿命が最大値をとる接線力係数の値は,円周方向の最大塑性流動量が0となる値に近いことを明らかにしている. 以上で得られた結果をもとに,第七章でころがり疲れ寿命の解析を行なっている.接触の繰り返しによって塑性流動が生じ,それにより加工硬化が起こると,今度は加工硬化が塑性流動に影響を及ぼすという,取扱いがやや面倒な系であるため,表面下の円周方向塑性流動に関する単純化したモデルを用いて,まず最大塑性流動量と加工硬化量について先に導いた実験式が,材料の加工硬化特性を介して関連づけられることを示している.ついでころがり疲れを表面下における塑性流動の累積による低繰り返し数疲れと考え,累積損傷仮説を援用して加工硬化を考慮したころがり疲れ寿命式を導き,ころがり疲れ寿命が表面下の最も損傷の著しい部分における疲れ破壊によってきまるという考えによって,寿命の接線力係数による変化が説明されることを示している. 第八章は結論で,本研究の主要な成果をまとめている. 以上を要するに,本論文はころがり疲れ寿命の接線力係数による変化を,繰り返し接触にともなう塑性流動および加工硬化と関連づけて説明したもので,工学上寄与するところが大きい。 よって本論文は博士(工学)の学位請求論文として合格と認められる. |